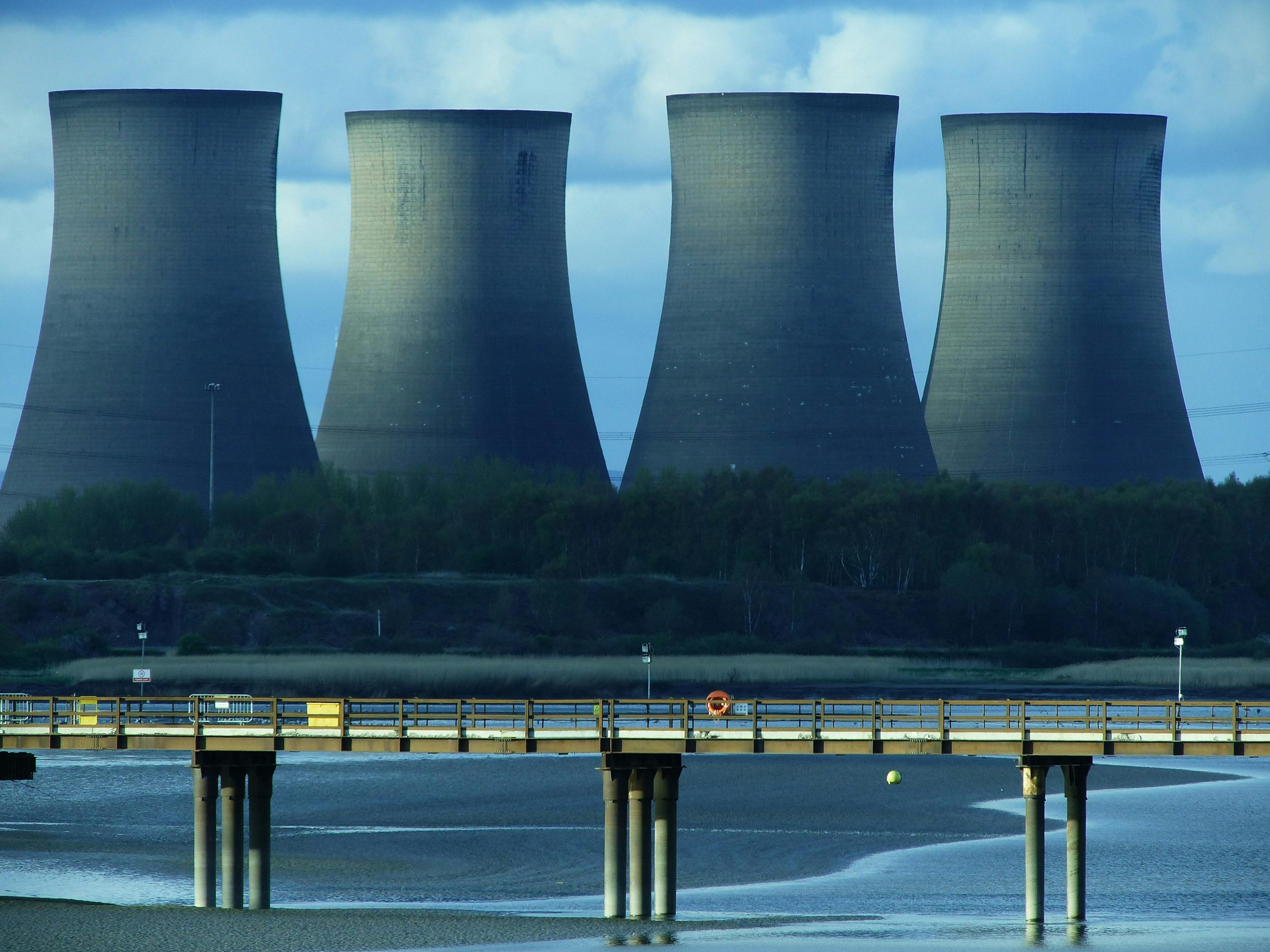
Powłoki specjalistyczne stanowią nieocenioną pomoc w wielu branżach, w tym w przemyśle motoryzacyjnym, energetycznym, lotniczym czy produkcyjnym. Dzięki swoim wyjątkowym właściwościom ochronnym i optymalizującym, powłoki te przyczyniają się do zwiększenia trwałości oraz wydajności urządzeń, zmniejszając koszty utrzymania oraz poprawiając efektywność operacyjną. W tym artykule przedstawimy 5 głównych zalet powłok specjalistycznych, które mają kluczowy wpływ na wydajność urządzeń.
1. Zwiększona odporność na zużycie
Jedną z najważniejszych zalet powłok specjalistycznych jest ich zdolność do zwiększania odporności na ścieranie i zużycie. Urządzenia przemysłowe, maszyny czy elementy silnikowe są często narażone na intensywne obciążenia mechaniczne, które mogą prowadzić do ich szybkiego zużycia. Powłoki ochronne, takie jak powłoki ceramiczne czy tytanowe, skutecznie chronią powierzchnie przed ścieraniem, co znacząco wydłuża żywotność komponentów.
Dzięki temu urządzenia mogą działać dłużej, bez konieczności częstej wymiany części, co przekłada się na wyższą wydajność urządzeń i mniejsze koszty utrzymania.
Przykład: W przemyśle motoryzacyjnym, powłoki specjalistyczne nakładane na elementy silników lub układów wydechowych zmniejszają zużycie i poprawiają efektywność pracy.
2. Ochrona przed korozją i czynnikami atmosferycznymi
Korozja jest jednym z najpoważniejszych zagrożeń dla wydajności urządzeń, szczególnie tych narażonych na działanie wilgoci, soli, wysokich temperatur czy agresywnych substancji chemicznych. Powłoki antykorozyjne, takie jak powłoki epoksydowe czy poliuretanowe, skutecznie chronią urządzenia przed tym niebezpiecznym zjawiskiem.
Ochrona przed korozją nie tylko zapobiega degradacji materiałów, ale także pozwala na utrzymanie wysokiej wydajności urządzeń w trudnych warunkach eksploatacyjnych, takich jak przemysł morski czy chemiczny.
Przykład: W elektrowniach czy rafineriach powłoki ochronne na rurach i zbiornikach zwiększają ich trwałość, zapobiegając uszkodzeniom związanym z korozją, co przekłada się na mniejszą awaryjność.
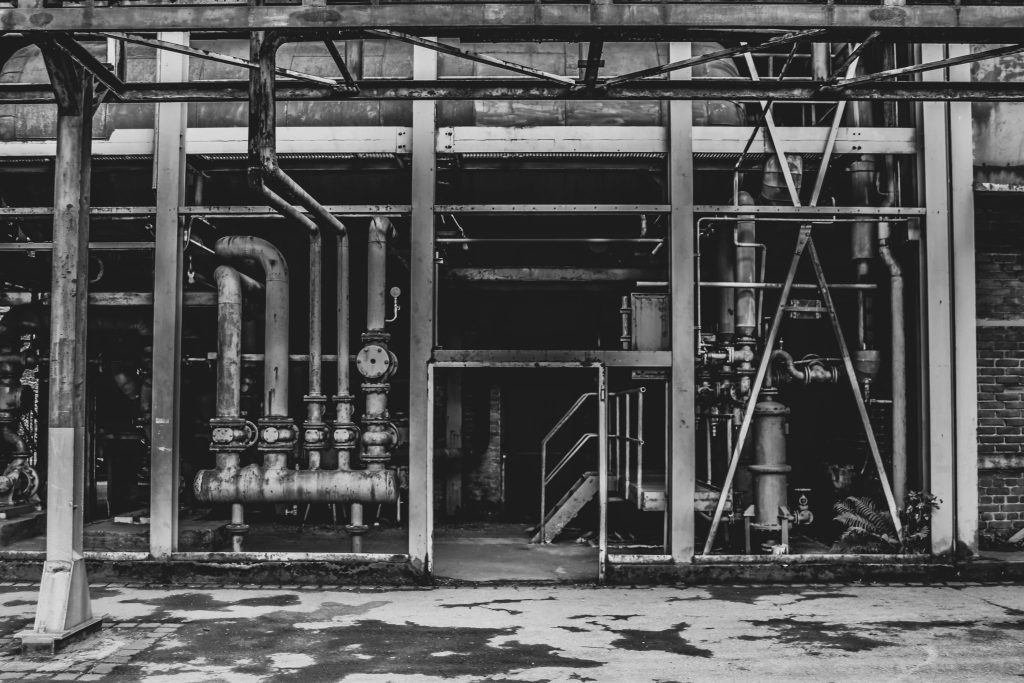
3. Odporność na wysokie temperatury
W wielu branżach przemysłowych, zwłaszcza w energetyce czy lotnictwie, urządzenia muszą działać w ekstremalnych warunkach temperatury. Powłoki termiczne, takie jak powłoki ceramiczne czy tytanowe, chronią komponenty przed skutkami działania wysokich temperatur, zapobiegając ich przegrzewaniu i uszkodzeniu.
Dzięki takim powłokom, urządzenia mogą pracować w wyższych temperaturach przez dłuższy czas, co znacząco zwiększa ich wydajność. Ponadto, ochrona przed wysokimi temperaturami minimalizuje ryzyko awarii i zwiększa efektywność energetyczną urządzeń.
Przykład: Powłoki chroniące przed wysokimi temperaturami są stosowane na turbinach gazowych, gdzie poprawiają wydajność silników i pozwalają na dłuższą pracę w trudnych warunkach.
4. Zmniejszenie tarcia i poprawa efektywności energetycznej
Powłoki specjalistyczne, takie jak powłoki PTFE (politetrafluoroetylen) lub DLC (węgiel amorficzny), mają właściwości zmniejszające tarcie pomiędzy powierzchniami. Zmniejszenie tarcia między ruchomymi elementami urządzenia przekłada się na mniejsze zużycie energii, a tym samym na wyższą wydajność urządzeń.
Mniejsze tarcie oznacza również mniejsze zużycie energii mechanicznej, co jest korzystne zarówno dla urządzeń elektrycznych, jak i mechanicznych. Dzięki powłokom zmniejszającym tarcie, urządzenia mogą działać bardziej efektywnie i oszczędniej, co redukuje koszty eksploatacji.
Przykład: W przemyśle motoryzacyjnym powłoki zmniejszające tarcie stosuje się w układach napędowych, co prowadzi do zmniejszenia zużycia paliwa oraz poprawy osiągów silników.
5. Zwiększona odporność na chemikalia i substancje agresywne
W przemyśle chemicznym, farmaceutycznym czy spożywczym, urządzenia często mają kontakt z agresywnymi substancjami chemicznymi, które mogą uszkodzić ich powierzchnie. Powłoki ochronne, takie jak powłoki fluoropolimerowe czy epoksydowe, skutecznie chronią przed działaniem substancji chemicznych, zapobiegając korozji i degradacji materiałów.
Dzięki takim powłokom urządzenia mogą pracować w środowisku o wysokiej koncentracji substancji chemicznych, co przyczynia się do ich dłuższej trwałości oraz wyższej wydajności w trudnych warunkach.
Przykład: W przemyśle chemicznym powłoki chroniące urządzenia przed działaniem agresywnych chemikaliów zapobiegają ich uszkodzeniom, co zmniejsza przestoje produkcyjne i zwiększa efektywność operacyjną.
Podsumowanie
Powłoki specjalistyczne odgrywają kluczową rolę w poprawie wydajności urządzeń, oferując ochronę przed zużyciem, korozją, wysokimi temperaturami, tarciem i chemikaliami. Ich zastosowanie nie tylko zwiększa trwałość komponentów, ale również przyczynia się do oszczędności energetycznych, redukcji kosztów utrzymania oraz minimalizacji ryzyka awarii. Dzięki tym innowacyjnym rozwiązaniom urządzenia mogą działać efektywniej, dłużej i z mniejszymi kosztami eksploatacyjnymi.
Inwestycja w powłoki specjalistyczne to krok ku bardziej efektywnemu i opłacalnemu zarządzaniu urządzeniami, który pozwala na pełne wykorzystanie ich potencjału.